
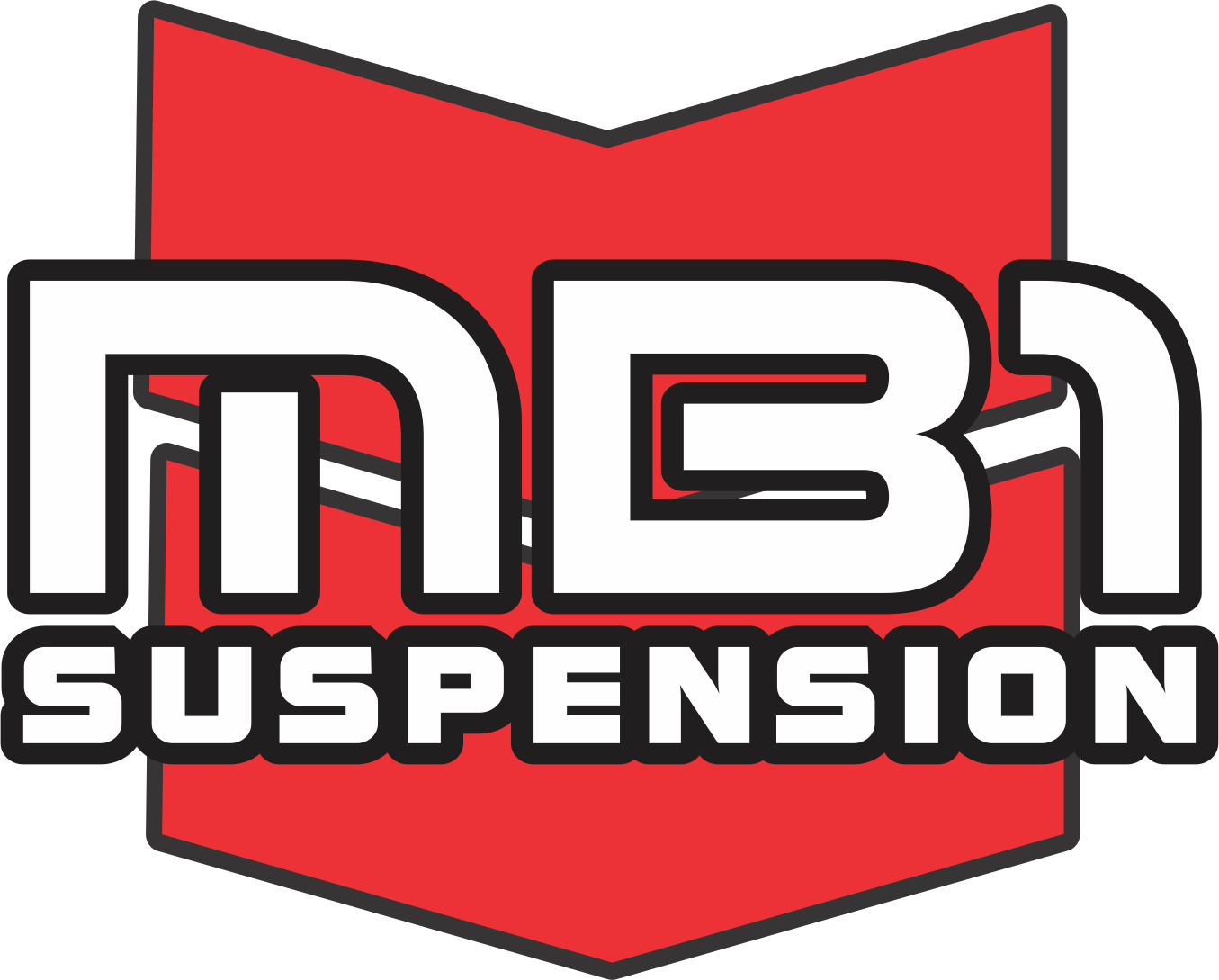






© Copyright MB1 Suspension 2018
Coatings
Motocross Suspension Coatings
Motocross suspension coatings have been a high tech and ingenious way of increasing component life of suspension, reducing heat build up, and reducing sliding friction of the fork tubes and the shock shafts on suspension. In the beginning at the Showa suspension facilities in Japan, there has been major modern breakthroughs in highly advance surface coatings. It involves a process known as Checmical Vapor Dempositon, Plasma Assisted Chemical Vapor Deposition, or Physical Vapor Deposition where surface engineers use ionic magnetron sputtering to take a gas state substrate (Titanium Nitride, DLC, Copper and Titanium Nitride) straight into a solid state known as deposition.The substrate is then attracted and bombarded to the electrically charged and magnetized object that needs to be coated with the substrate producing a coating that covers the object uniformly in the substrate and is only microns thin for virtually no geometry change noticeable at all. In the beginning at the state of the art coating facilities in Japan, surface engineers have been able to incorporate a coating known as Titanium Nitride to sliding motocross suspension lower fork tubes and shock shafts. MB1 Suspension has successfully used titanium Nitride coatings on his suspension in order to increase the durability of his suspension systems and at the same time decrease sliding friction in order to give the suspension an improved feel for the terrain underneath it. Titanium Nitride, an effective and successful addition to suspension components, was at one point the cream of the crop in terms of suspension coating advancements and also the pinnacle of latest surface treatments to enhance performance of suspension action over rough terrain. But as time passed by surface engineers realized that there was a better coating with even greater performance values that would blow Titanium Nitride coatings out of the water in terms of numbers on a spreadsheet but not so much in terms of real Motocross racing application use. The new coating that was starting to be developed is called DLC or Diamond Like Carbon coatings. DLC coatings have a lower coefficient of friction than Titanium Nitride coatings and because the coating contains a Nano crystalline structure and carbon elements in it, the coating lasts considerable longer than Titanium Nitride coatings because it has a much harder surface to it. But even though DLC on paper has a better track record over Titanium Nitride, that does not mean that DLC dominates Titanium Nitride out in the field and race environment. Standard Titanium Nitride comes in a natural gold color but the special variant of Titanium Nitride coating that the riders prefer is known as Turquoise Titanium Nitride. Turquoise Titanium Nitride is harder to form than standard Titanium Nitride and has less friction because it is a thinner coating as a result of the copper infusion oxidizing process and specific voltage treatment process added to the standard Titanium Nitride procedure to form Turquoise Titanium Nitride. Turquoise Titanium Nitride has iridescent properties, is more expensive than standard Titanium Nitride, is softer than DLC as well as standard Titanium Nitride making it slicker and therefore also allowing it to be polished better giving the coating less friction than DLC, standard Titanium Nitride, and ultimately allows the coated suspension to slide with minimal resistance, is rarer than standard Titanium Nitride and DLC, has enhanced feel and sliding properties for the terrain versus standard Titanium Nitride and DLC. The only downside to Turquoise Titanium Nitride is it does not last as long as DLC and wears out a little bit quicker, especially if riders use the coating on sandy track conditions. But the strengths outweigh the weaknesses and as an added bonus Turquoise Titanium Nitride is by far more exotic and beautiful looking than standard Titanium Nitride and DLC coatings. The Turquoise Titanium Nitride is a coating that can bring true luster and unmatched brilliance to your personal motocross bike. Another coating known as Kashima coating is a patented Japanese coating that is used on aluminum and other porous materials to decrease friction and reduce heat build up that would result in suspension "fade". Showa and Kayaba apply the dark race works bronze colored Kashima to the upper fork tubes and shock body that are found normally only on A-kit suspension and full blown works "factory" level suspension packages to allow the suspension to feel virtually the same from beginnning to end during use in terms of performance even after a hard straight thirty plus minutes of riding on the suspension.